Table of Contents to MTD
- MTD 2025
- April 2025 – Making Roads and Streets and Roads
- March 2025 – Modeling Paints
- February 2025 – Gerry Glancy on Tortoise Switch Machines.
Making Roads to Streets and Roads
This month’s modeling demonstration was focused on “Making Roads” which morphed into “Streets and Roads”. The “Streets” portion of the discussion focused on the Walthers Cornerstone Street systems in asphalt, concrete, and brick. Glenn Runkewich used the asphalt system on his layout. The difficulties are as found in any pre- manufactured product that needs to be kit-bashed to form your idea. The kit paving pieces have a molded in crown and a curb at the outside edge.
Glenn found these points to the system:
THE GOOD
Modular – many configurations
- intersections and curves
- can be kit-bashed
Details – sidewalks, curbs, manholes, drains, driveways, fire hydrants
Pavement – asphalt, brick, concrete, crown and gutters
THE BAD
- streets not roads
- seams hard to hide
- crown complicates kit bashing
- pricey
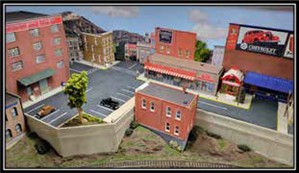
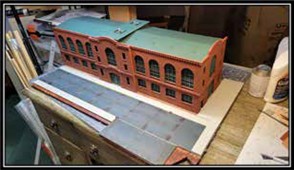
The top photo shows a more typical street installation. On the bottom photo an alley way was made by turning the street section. The left photo shows an installation along a street where the crown molding and curbs needed to be cut down. This leaves the regular pattern on the street that will be difficult to hide. What is notable about this product is the fine-grained asphalt texture. A box of parts was passed around for the participants to observe.
Gerry Glancy brought in a similar set of street parts in the concrete finish so the differences could be seen. Glenn Gibson noted that he used the brick pattern set for his Trinidad streets.
It was suggested that the joints could be filled with Glass Gallery Leading. This is a liquid product, or sold in strips. It is a bright product, but can be painted. It can also be used on roofs at the edge and around roof accessories to mimic the tar bands commonly found near roof openings.
Gerry Glancy showed us the street track inserts, also from Walthers, that can be used to bury tracks running in streets. These are concrete colored panel pieces to fit Atlas snap track in a number of straight or specific curved pieces. The side panel pieces are molded to fit over the spike detail adjacent the rail for a tight fit. Turnouts are accommodated by specific pieces that fit up to Atlas snap track turnouts.
Rich Gibson and Mark Shifter tag teamed the presentation on roads. As “they have gone down the same road” using EVA foam cut to width on their respective layouts. This material is available in varying thickness, but the presenters use 2 mm thickness. The material is available in sheets and rolls. It is capable of being cut to any shape for roads or parking areas. It accepts paints and weathering. It can be striped with paints by masking the line and painting. There was a spirited discussion of wheel paths on the asphalt surface. Why are the paths sometime whiter and other roads darker? The prevalence is for dark wheel paths due to tire wear. The surface of the road has some variation and yields differing wheel path colors. Mark uses the foam material for his concrete roads and gutter pans by painting the material grey and weathering it to a concrete patina.
Another method for a road surface is to use joint compound to build up a road section. This material always cracks so it is a natural road material. It is difficult to get a smooth uniform surface on the first try, and subsequent applications will have a different texture and color. Rich Gibson brought a couple of examples from his previous layout to show.

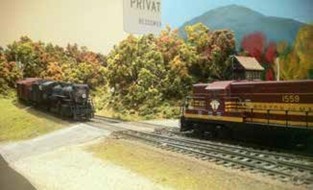
While not really visible in these small photos, there are areas of differing texture along the edges of the roadway. Mark Shifter showed the Micron Pens that he uses to make cracks and joints in the roadway. These are art pens available in a variety of tip sizes and he uses the 0.05 mm size for his work.
The use of Woodland Scenics paving tape was discussed as the edge form for the roadway. This works good for the edge but needs to be removed soon after completion. The use of styrene strips for curbs was also noted. This allows for curves and shapes along the roadway.
Finally, the subject of gravel or dirt roads was discussed. Rich Gibson uses a combination of natural materials to use as paving material. Mark Shifter uses fine sand but mostly un-sanded tile grout from Home Depot. This material is available in a variety of colors and is very fine-grained to mimic the weathered gravels found on roads.
It was also noted that the gutter sands can be screened to find a variety of sizes and re- used as model road surfacing.
Utilizing roofing shingles as a surfacing material was noted. It does not seem that any of the group had tried this yet. Preprinted road material is available in rolls, but curves are limited to a fixed radius. One technique that had been used is the captured Google Earth road images, resized, and stitched together in Photoshop. This gives the modeler all the road appurtenances and authentic crack patterns for your model road.
Modeling Paints
The second installment of the modeling demonstration was hosted by Rich Gibson on Modeling Paints. He started the discussion by noting that using solvent paints like Floquil in an airbrush was too difficult to clean up. He transitioned to Polly S Railroad Paints, and they have been discontinued. Many modelers maintained a supply and have been using the supply until exhausted. He has been using rattle can paints.
Rustoleum Camouflage Brown is used for track painting. The khaki may be used as an aged concrete color. Ace primer colors are used for other work. Grey is the tree trunk or asphalt shingle color and red for brick buildings or large rust patches. Tamiya primer is the go to product for priming structure kits, particularly the resin kits. It comes in a variety of colors. Rich still has some Scale Coat spray cans and uses this on metal items. This includes brass car sides, locomotives, and brass detail parts. The line has been discontinued and although a new owner has been rumored, no items have been produced. There was a discussion on decanting paint from spray cans for use in an airbrush or brush painting. The general consensus was that this was okay for touch up brush painting but was not a good idea for airbrushing. The reason for this was conjectured that the problem was with spray can nozzles that were not producing a consistent spray pattern. Rich indicated that he has increased his use of craft paints. He uses this on wood structures with a dry brush to pull out the grain of the wood. For
railroad specific colors, Rich has been using Tru Color paints. These colors are accurate for Maine Central paints. They also have a range of boxcar reds. This lends variation to the fleet. Using these paints yields a nice glossy finish so no gloss coat is necessary for detailing the car. Gloss coating can be done with Pledge floor polish that used to be called Future floor polish. This yields a good gloss coat with a minimum of cost. Clean up can be done with Windex or windshield washer fluid. To cut the gloss, the models can be coated with Testors Dull Coat. Mark Shifter noted that he has moved away from using an airbrush. He uses the rattle can paints on his rolling stock, and structures. He is using inexpensive acrylic paints for his backdrops and other scenery work. He is using wood or Masonite to clean the paint off the track and further to clean the track regularly. It was mentioned that 3 in 1 oil can be used on the top of the track prior to painting. This allows for easy clean-up after painting. This requires care to avoid applying too much oil resulting in the oil soiling the web.
As somewhat of a counterpoint to painting, Glenn Gibson brought in his latest modeling efforts. These were all Walthers plastic kits. The Cornerstone Industry Office was the first structure shown. He used rattle can paints to color the structure prior to weathering. This structure is molded in yellowish plastic and the paints turned into a convincing brick and wood tone structure.

The Cornerstone Rural Grain Elevator was not painted. The structure was dull coated and weathered with powders.

The Cornerstone storage shed was again weathered with powders and detail painted to bring out the different materials.
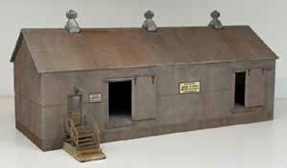
Gerry Glancy on Tortoise Switch Machines
Gerry Glancy, being ever the pioneer, presented the initial modeling topic on Tortoise switch machines. These are the stall motor devices for throwing turnouts on the model railroad. They can be activated by switches, DCC accessory decoders, or an AC steering diode arrangement. These have been available for about 40 years. There have been some changes due to changes in suppliers for the circuit board and the edge connectors available. The modeler needs to be aware of this as older versions can still be found in the marketplace. The flimsy wire that is supplied with the machine is not suitable for most installations. A heavier gauge music wire or piano wire should be used and is available from Ace hardware in a 0.032 or 0.039 thickness. The wire is bent to the proper shape and with practice this becomes automatic. The holes in the Tortoise need to be enlarged for the larger gauge wire with a twist drill. A template for drilling and positioning the Tortoise should be used for alignment.
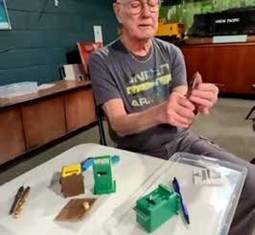
There are commercially available templates, use the paper cut out from the instructions, or make your own from styrene. Gerry would recommend a brad point drill in 3/8 inch for making the benchwork hole. The brad point helps to keep the bit from wandering as you start the hole. A DeWalt set of brad point drills is available from Home Depot, Lowes, or Ace Hardware. To aid in installation, it was recommended to use a light as a cell phone light over the hole to show where the wire should be fed. The replacement wire is much harder than normal, so it is best to use a dedicated pair of heavy cutters or a cut off tool to trim the wire. There was discussion on the location of the throw rod, and it was suggested that using the offset end of the switch throw was better than the center of the throw bar. To help in positioning the unit below the benchwork, use hot glue on the face of the machine to hold it in place and yet allow some final positioning to take place.
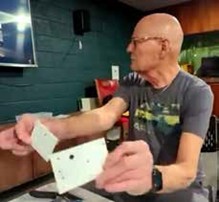
To enlarge the footprint of the Tortoise, it can be mounted at the work bench on a 4 x 4 or a convenient size piece of Masonite, styrene, or plywood, and then the assembly may be mounted to the benchwork with screws positioned away from the machine itself. The Smail is another version of the switch machine with a DCC accessory decoder built in. This can then be programmed as an accessory on the layout and controlled by the DCC throttle. This unit cannot be wired for indicator lights. These should be programmed prior to installation to allow the use of the programming track. Tortoise may be added after the fact on the layout, by modifying the head block ties, drilling the hole, remounting the ties, and completing the installation.
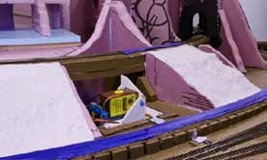
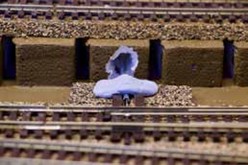
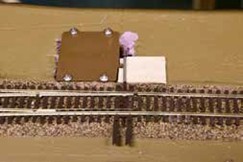
Alternatively, the machines can be surface mounted as shown in Scott Ogle’s installation.
Gerry noted that a track short is encountered when using the tortoise to power the frog. The internal switches on the tortoise can be activated prior to the points leaving contact with the powered rail. By adjusting the throw wire this difficulty can be prevented. The modeler needs to be aware this can occur and that there is a fix.
If the modeler has access to a 3D printer there are files for remote control inserts and other accessories on: https://www.thingiverse.com/.
Rich Gibson noted the machines may be mounted to foam with caulk. He further noted there are few reasons to have powered switch machines on a model railroad. If the turnout is not accessible, it is a good idea to power the throw, or in the case of CTC control for the layout, it is necessary to allow the switch control to be triggered remotely. Wally indicated that all the railroads he worked on the switches were thrown manually.
Rich Gibson has located a lower profile switch machine from: https://modelrailroadcontrolsystems.com/. They are located in Mountain View, California and have a reasonable shipping policy.
Hankscraft Switchmaster motors were mentioned but they are supplied by: http://www.builders-in-scale.com/bis/sm-home.html. The website notes they are moving out of storage, so the editor is not certain how available they may be. Servos were noted as being available to perform the switching duties. These are very flexible as the throw distance is adjustable. They are readily available in hobby stores that focus on radio control hobbies.